Расширение линейки шиномонтажного оборудования Bosch
Компания Bosch представляет расширенную серию шиномонтажных станков, спроектированных с применением расчёта по методу конечных элементов.
Казалось бы, шиномонтажное оборудование — это «классика» автосервисного оборудования, где все давно придумано и изобретено. Да, появляются автоматизированные роботы, которые выполняют всю работу по шиномонтажу почти без участия человека, но разве что–то можно усовершенствовать и улучшить в обычном шиномонтажном станке?
Оказывается, можно! Особенно, если использовать современные технологии конструирования и компьютерное моделирование. И инженеры Bosch в очередной раз это доказали. Они проанализировали существующие технические решения в шиномонтажном оборудовании и выявили ряд направлений, в которых эти конструкции можно улучшить.
1. Точность работы
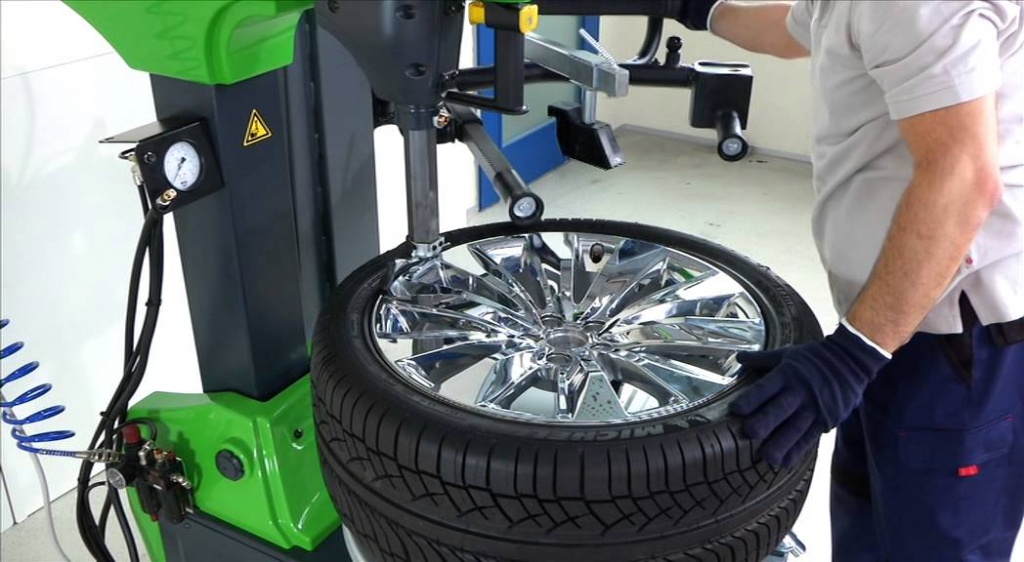
Колесные диски современных автомобилей стóят подчас очень дорого. Повреждение или даже небольшие царапины на них в процессе шиномонтажа — недопустимы. Для этого монтажная головка должна базироваться относительно колесного диска очень точно и с небольшим гарантированным зазором. С появлением современных низкопрофильных шин и шин с жесткими боковинами (RFT) выполнить это требование на обычных станках стало значительно труднее. Различного рода пластиковые защитные накладки спасают ситуацию, но лишь частично.
Кардинально решить вопрос точности можно лишь решив следующую задачу:
2. Прочность и жесткость.
Шиномонтажный станок — довольно габаритная конструкция, причем основные рабочие элементы — монтажный стол и монтажная головка не прикреплены непосредственно друг к другу, а кинематически связаны через множество элементов. При этом монтажная головка должна перемещаться относительно стола по вертикали и горизонтали, а сам стол вращаться.
3. Надежность и долговечность.
Все элементы станка испытывают при работе значительные нагрузки. От того, как станок будет противостоять (сопротивляться) этим нагрузкам зависит и срок его службы. В случае ошибок в этих расчетах через некоторое время силовые элементы могут не выдержать и деформироваться, разболтаться или лопнуть по сварочным швам.
Новое решение
Проанализировав эти проблемы, инженеры Bosch создали математическую модель и произвели расчеты.
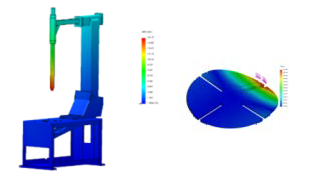
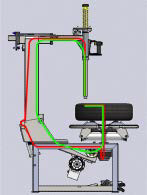
В сопромате известен расчет методом конечных элементов, который использует анализ нагрузок силовых конструкций, основанный на рассмотрении конструкции как совокупности типовых элементов, называемых конечными элементами (КЭ). В этом случае учитываются не только сами элементы, но и связи между ними.
В результате этого расчета инженеры шиномонтажных станков Bosch пришли к мысли о необходимости кардинального изменения конструкции и, в первую очередь, в повышении жесткости всей конструкции станка. Для этого была разработана новая структура, так называемая G-frame. G — потому что действующие на шиномонтажном станке силы действуют по траектории, напоминающей латинскую букву G.
Одним из важных технических решений было закрепление откидной монтажной колонны в новом месте. При этом традиционные функциональные элементы станка теперь стали еще и элементами жесткости. Таким образом, удалось добиться значительного снижения предрасположенности различных компонентов стенда к деформациям, вызываемым действующими силами. Повышение жесткости станка позволило решить главную проблему — точное базирование, что значительно снизило риск повреждения дисков при выполнении монтажных/демонтажных работ.
Конструктивные изменения:
|
|
|
Изменение точки опоры колонны: усиленная опорная ось перенесена ближе к столу, на переднюю часть колонны | Функциональные компоненты станка стали также элементами его жёсткости | В движение монтажную колонну приводит увеличенный пневматический цилиндр диаметром 100 мм, закрепленный в задней части колонны |
Станки от модели TCE4430 и старше имеют увеличенное сечение монтажной колонны — 140 х 140 мм.
Благодаря техническим изменениям станок не только приобрел дополнительную жесткость, но и стал работать быстрее, а взаимодействовать с ним оператору стало проще.
Точный анализ
Метод конечных элементов позволил точно оценить силы, которые действуют на элементы шиномонтажного станка в реальной жизни, и определить зоны, наиболее подверженные напряжению, зоны, где существует наибольшая вероятность поломки. Вероятно, это первый шиномонтажный станок на рынке, который разработан с применением анализа методом конечных элементов. В процессе конструирования были проведены многочисленные тесты, в ходе которых к станку прикладывались силы, в 10 раз, превышающие те, что действуют на станок в обстановке шиномонтажного центра.
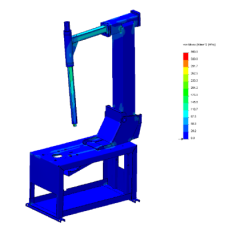
Научный подход
- Использование технологий конструирования и методов контроля качества, повсеместно применяемых в автомобильной промышленности;
- Широкое применение таких инструментов, как метод конечных элементов, и новых концепций (например, бионический дизайн и DFM);
- Открытый и глубокий анализ каждого компонента для оптимизации конструкции и придания ей качеств, отвечающих требованиям покупателей;
- Анализ по методу конечных элементов (FEM — метод анализа сил в системе и цветового представления сил в зависимости от ихх величины.);
- Определение реальных сил, действующих на детали шиномонтажного станка. Анализ критических областей;
- Тесты с приложением сил, в 10 раз превышающих нормальные, для определения деформаций элементов и их пределов прочности.
- Исследования сил, действующих на элементы станка, в лабораториях Миланского Университета;
- Исследования сил, действующих на станок при монтаже шин (проведено WDK);
- Измерение деформаций (на заводе Sicam).
Испытания
При разработке этой серии станков внедрили новые требования к надежности. Станок прошел испытания, эквивалентные его бесперебойной работе в течение 5,5 лет. Причем шиномонтажный сезон во время этих испытаний продолжался круглый год. Если сравнивать с пробегом автомобиля, то данный тест равносилен миллиону километров пробега машины. Каждый ответственный элемент станка был подвергнут предельным нагрузкам, прежде чем он занял свое место.
Особенности и преимущества линейки G-Frame
Особенность | Преимущество |
---|---|
Жёсткость и надёжность: |
|
G-образная структура: повышение жёсткости конструкции за счёт сокращения длины нагруженных элементов. | Предотвращение повреждения шины и колеса благодаря высокой жёсткости конструкции. |
Сечение наклонной колонны: 140x140 мм. Диаметр пневматического цилиндра, приводящего её в движение: более 100 мм. Имеется демпфер. |
Простой монтаж и демонтаж шины, высокая скорость работы. |
Возможно, первый станок на рынке, конструкция которого полностью рассчитана с применением метода конечных элементов. | Достижение максимальной жёсткости станка путём повышения толщины стенок и увеличения поперечного сечения деталей именно в тех местах, где это необходимо. |
Эффективность и простота использования: |
|
Механизм отрыва борта снабжён клапаном сброса давления. | Скорость отрыва борта выросла на 40%. |
Сечение наклонной колонны: 140x140 мм. Диаметр пневматического цилиндра, приводящего её в движение: более 100 мм. Имеется демпфер. | Высокая жёсткость снижает необходимость в ручной коррекций положения шины при монтаже. Что дает простоту использования и быструю работу. |
Ускорения накачивания шины на 25% по сравнению с основным конкурентом. | Быстрая накачка шины. |
Новая конструкция пневматического узла рабочего стола. |
|
Двигатель с электронным управлением (мотоинвертер). | Две скорости, управление с помощью педали. Кроме того, нет блокировки стола на высокой скорости работы — автоматические замедление стола и повышение момента. |
Новая конструкция зажимных кулачков. |
|
Модульная конструкция. | Лёгкое обслуживание, возможность модернизации. |
Вот такой прогрессивный подход для достижения наилучших результатов был реализован при разработке (занявшей около 2 лет) этого, на первый взгляд, весьма консервативного гаражного оборудования.